- ● Product List
- Tungsten Carbide Drawing Dies
- Tungsten Carbide Wire Drawing Dies
- Tungsten Carbide Bar Drawing Dies
- Tungsten Carbide Tube Drawing Dies
- Tungsten Carbide Tube Drawing Dies Plug
- Carbide Rolls
- Carbide Roll Rings
- Grooved Roller
- Roll Rings for High Speed Rolling of Ribbed Steel Bars
- Wire Guide Die
- Powder Coating Die
- Peeling Dies
- Custom Drawing Dies
FAQ
Carbide drawing dies will generate different wear and tear during stretching process. The unreasonable hole structure, different axis of steel bushing and mould core, low processing ability, unreachable technical standard and problems existing in the drawing process can change the stress state of the wire drawing mould. We summarize the some phenomena often encountered as follows
1. Wear of Ring Groove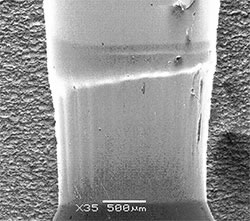
Ring Groove
Through the observation of after-use carbide drawing dies, we find that the entrance of working area of more than 80% wire drawing moulds has a ring type groove which is more serious abrasion than other parts. It is widely used in drawing wire industry.
ReasonsStrong friction on the mould wall causes the tungsten carbide particles to gradually peel off and form rough surface. The rough surface scrapes off the metal scrap from the wire surface, which makes the lubricating conditions worse and increases the wear rate, finally result in die wall to form ring groove. There is a constant speed along the axis before drawn material getting into the working area. At the moment of deformation when the drawn body is just entering into the work area, the rate and direction is changed and the vortex of speed is formed. It is like the liquid flows to be blocked and has scouring effect on its impediment. The working area is eroded, thus causes the abrasion of die wall. The grinding line of ring groove wear is formed.
SolutionSlight abrasion of ring groove can be regarded as normal wear, but the serious wear should be properly increased counter pull or cut down the angle of the working area.
Drawing marks refer to groove marks that in line with the stretching direction.
1. The stretched marks are affected by the abrasive wear of ring groove.
2. The angle of the working area is too small or the draft of the steel is too big.
3. There is oxidized trace on the wire surface, which is not implemented good surface coating treatment before drawing. The uneven surface steel wire has more occlusive effect on the die wall, which enlarges the friction between the wire surface and mould wall, thus resulting in wolfram carbide particles to peel off.
4. The property of the lubricant does not match with the type of the drawn steel wires and the conditions of stretching technology. Additionally, the coating thickness of the wire surface is insufficient, and the ability of catching lubricant is reduced, thus leading to bad lubricating effect.
5. Rough mould surface and insufficient degree of finish make the friction between steel wires and die wall increase.
1. To improve the surface treatment technology before drawing the steel wires.
2. To choose proper lubricant
3. To increase the surface smoothness of the carbide drawing dies.
There are metal sheets with different sizes firmly attached to the top of the position where steel wire and mould wall in the working area of the wire drawing mould firstly contact, this is called seaming phenomenon.
The surface is unclean before drawing the steel wires, so there is residual oxidized iron sheet. This is the main reason that caused welding damage.
SolutionWire manufacturers should make great efforts to improve the surface treatment in order to avoid bringing the oxide scale.
Different axis wear refers to that the wire diameter will appear a certain out-of-roundness after the die hole is worn unevenly.
1. The out-of-roundness is very poor and the die wall is stressed unevenly. The mould wall is suffered a large force at the large diameter side and the friction will be increased correspondingly. Therefore, the wear and tear is larger than that of the small diameter side.
2. The steel jacket and mould core is not the same shaft.
3. Carbide drawing dies are put wrong position on the drawing machine, which makes the mould and steel wire in different axis, leading to unilateral abrasion.
4. The partial density of inner hole of the wire drawing mould is uneven, which results in uneven surface smoothness of the processed dies. The partial fineness is poor due to large friction coefficient, thus leading to fast abrasion.
1. If the abrasion of different axis appears in the first die, it only can start with the dimensional accuracy of the wire preform.
2. If the intersecting position of the working area and lubrication area is not at the same level, the quality of button die will naturally have problems, so the processing technology of button die should be improved.
3. If the working area and the lubrication zone intersects at the same level, but the wear position is on different level. The carbide drawing dies are put incorrect position on the drawing machine.
- Tungsten Carbide Wire Drawing Dies
- Tungsten carbide wire drawing dies have a certain shaped hole in the center, including round, square, octagonal or other special ...
- Peeling Dies
- Tungsten carbide peeling dies have different specifications, such as round, square, hexagonal, deltoid and other custom shapes ...